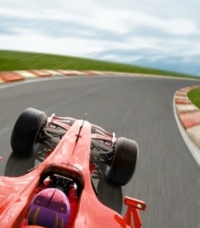
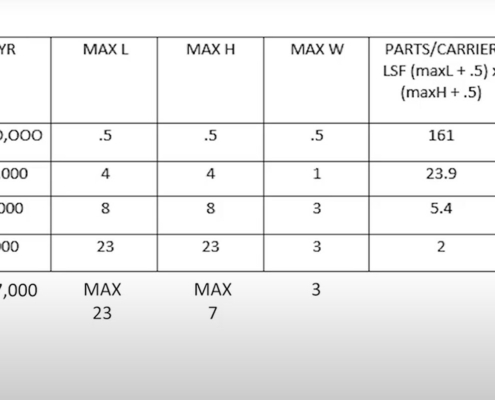
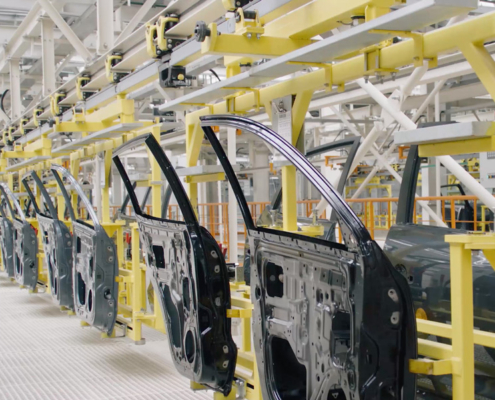
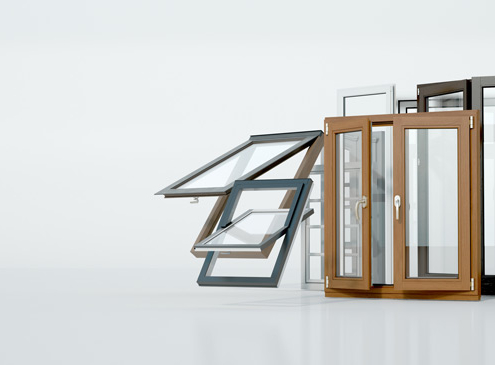
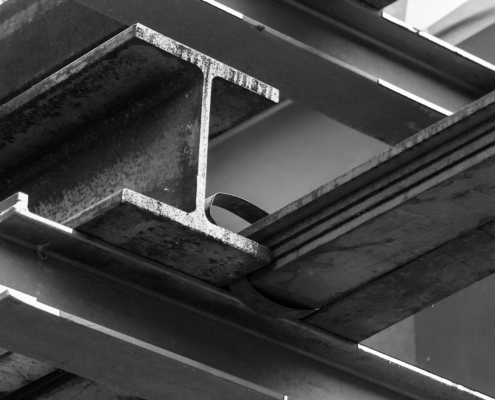
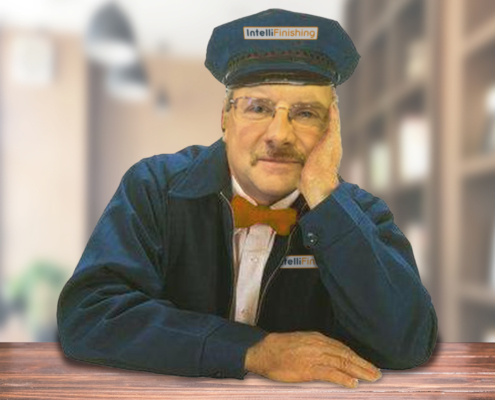
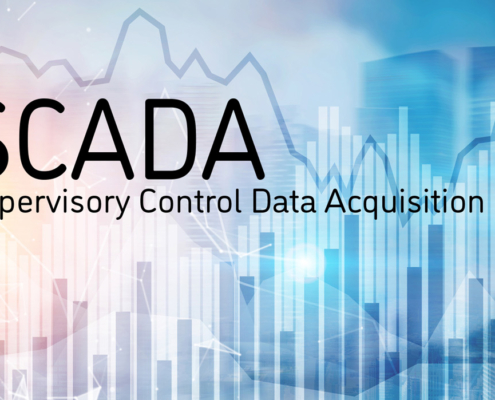
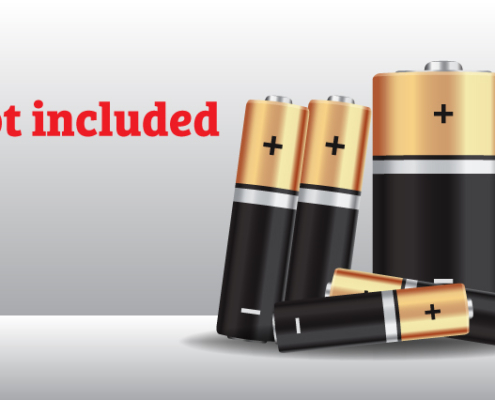
*Batteries Not Included: Explore What Comes with Automated Finishing Systems Before You Purchase
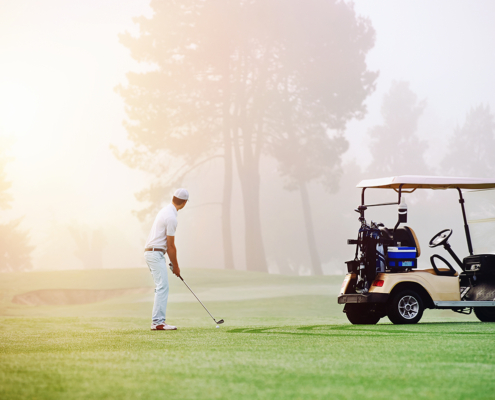
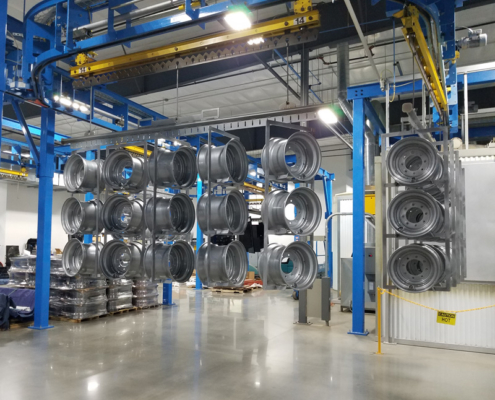
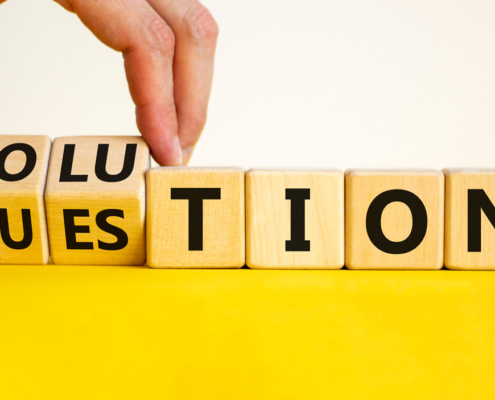
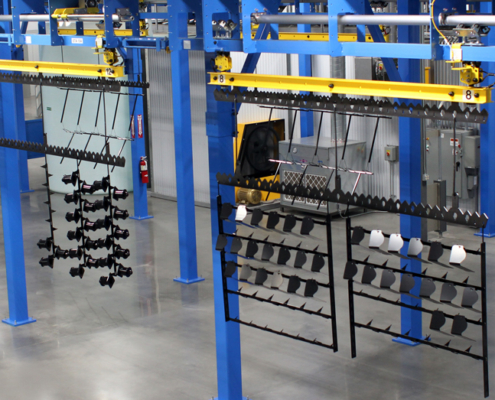
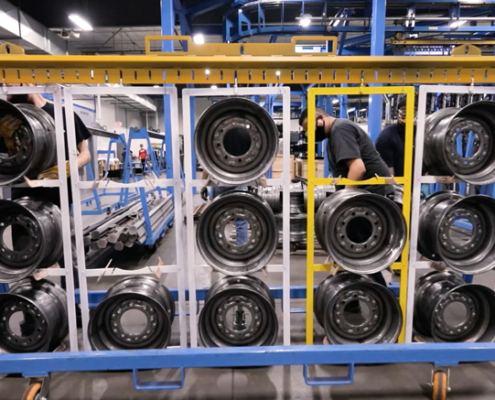
IntelliFinishing Systems and Part Density Go Together Like Eggs and Bacon, with Racking as the Gravy on Top
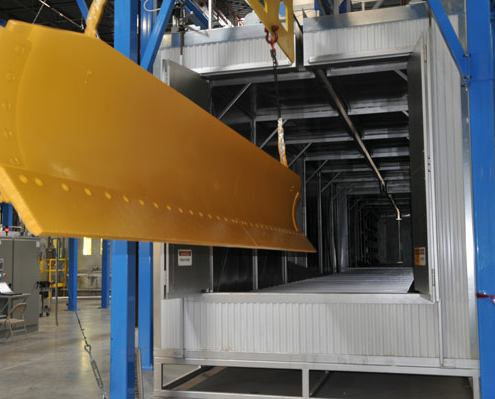

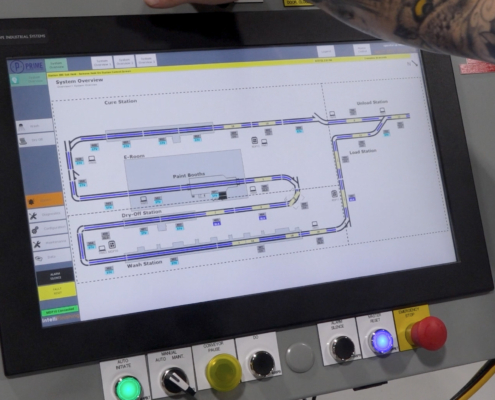
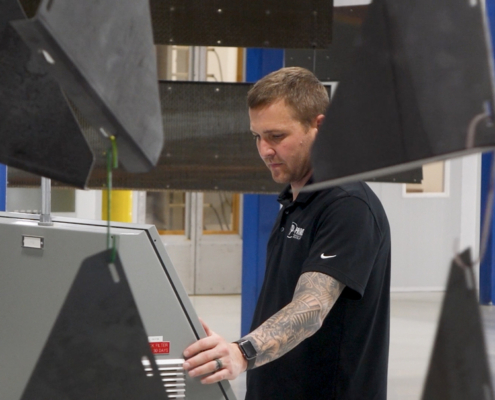
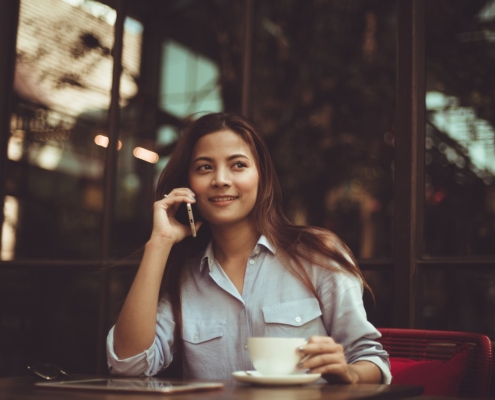
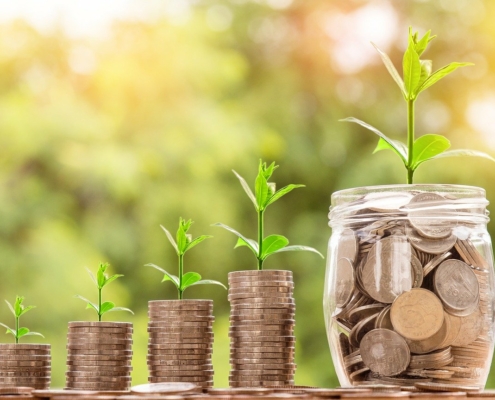
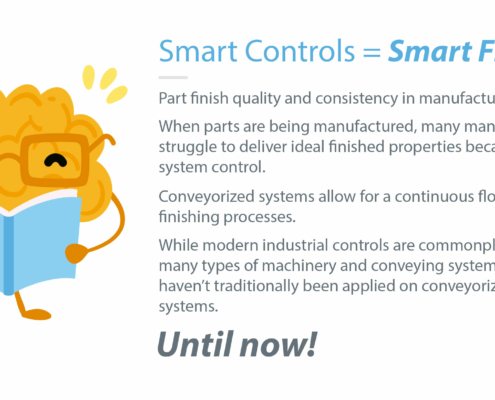
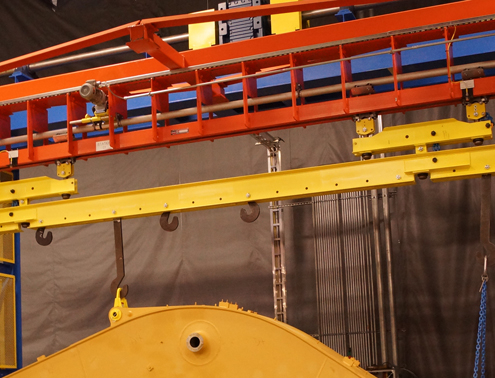
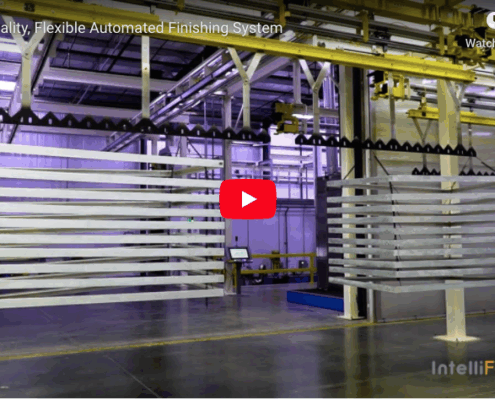
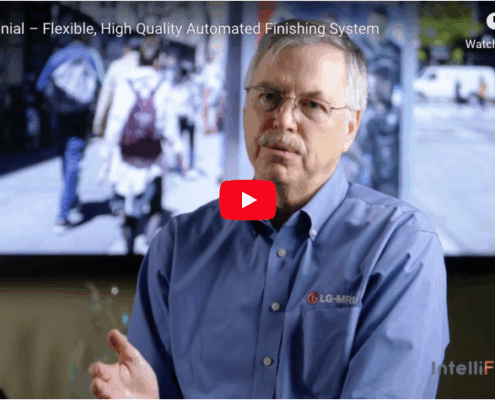
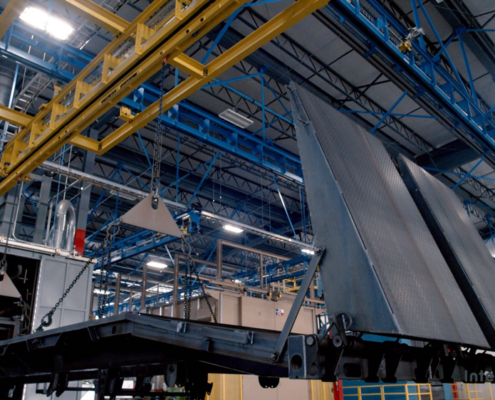
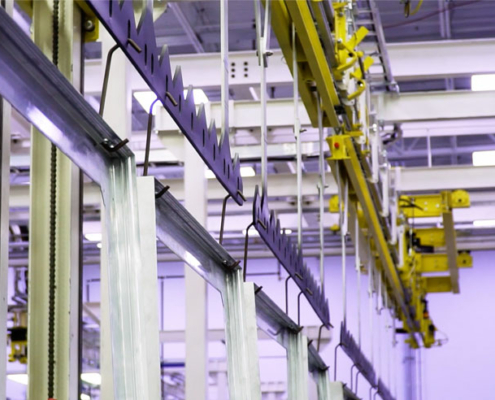
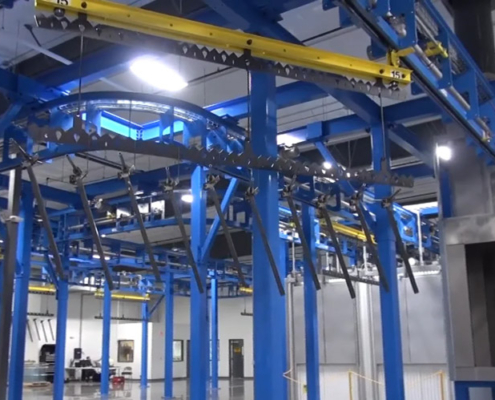
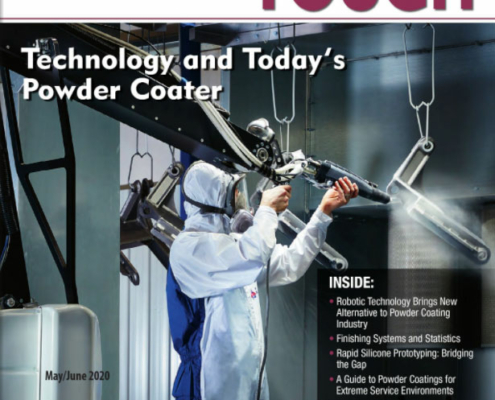
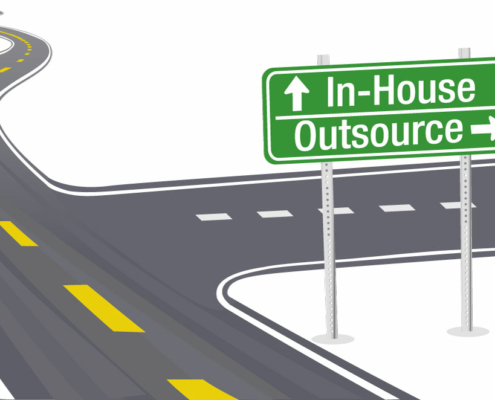
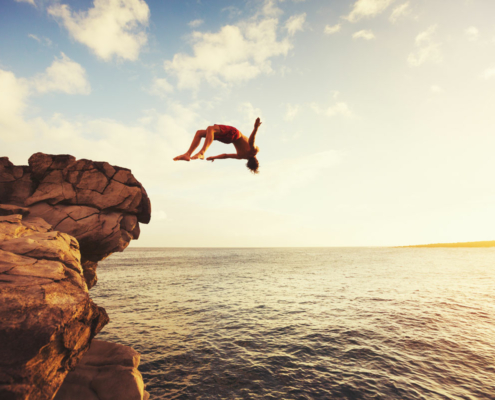
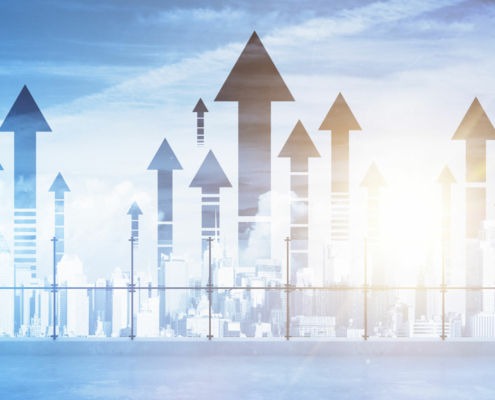
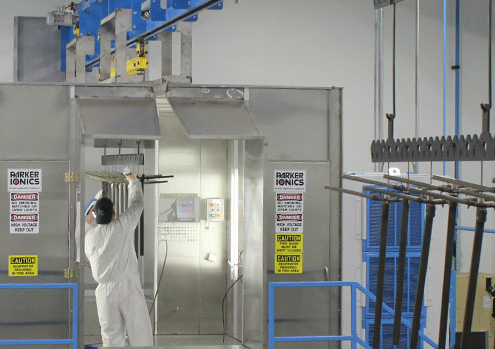
JR Custom Metal Products Further Elevates Operations and Efficiency with IntelliFinishing System
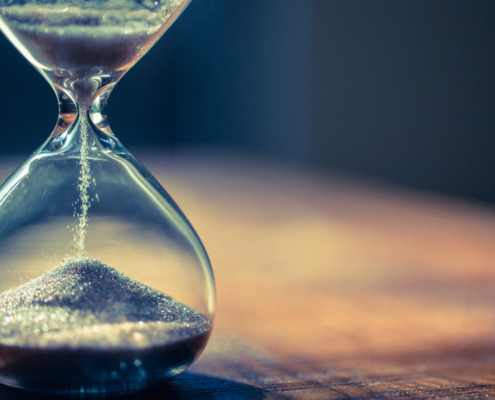
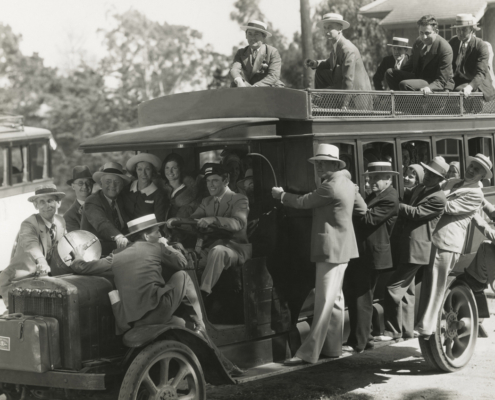
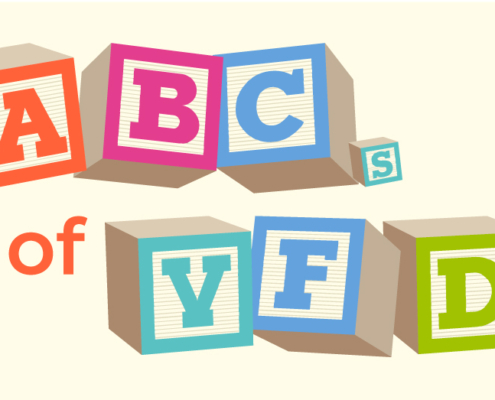
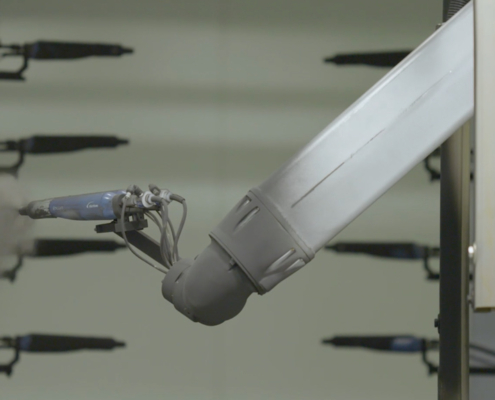
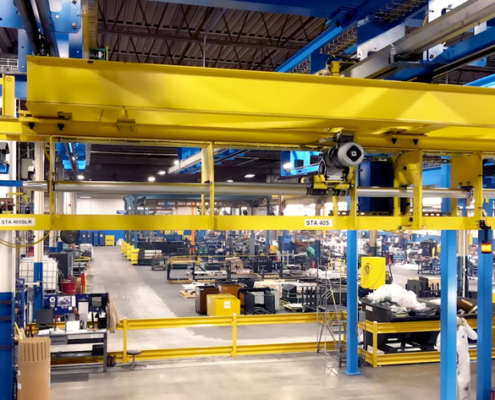
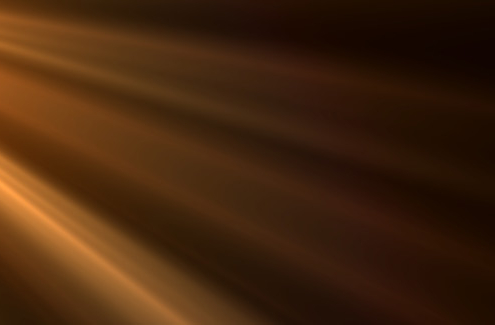
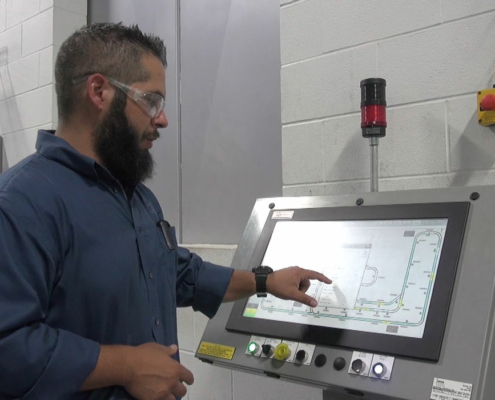
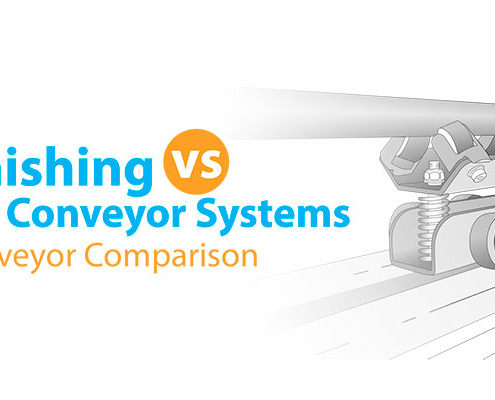
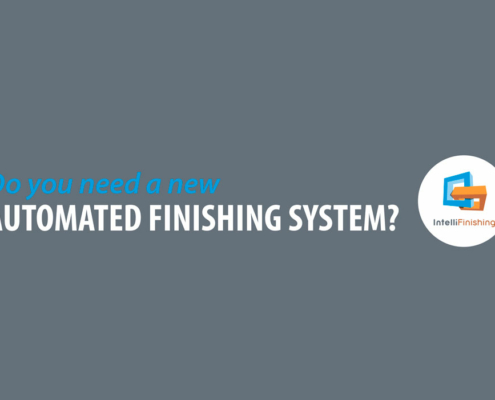
Infographic Will Help You Start to Determine the Best Type Automatic Finishing System to Consider
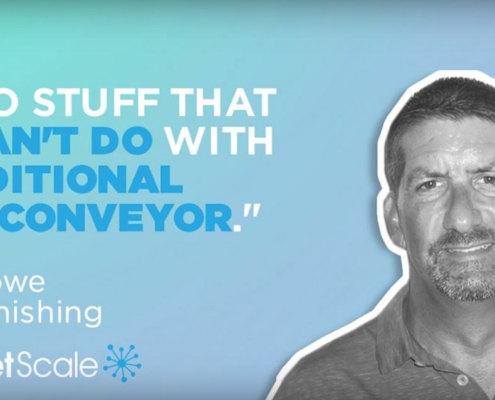

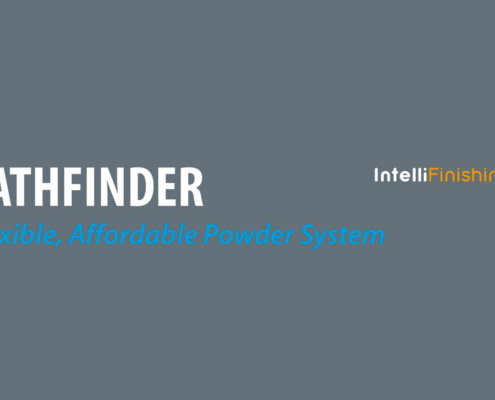
Introducing The Pathfinder – A Complete, Automated and Affordable Flexible Powder Finishing System
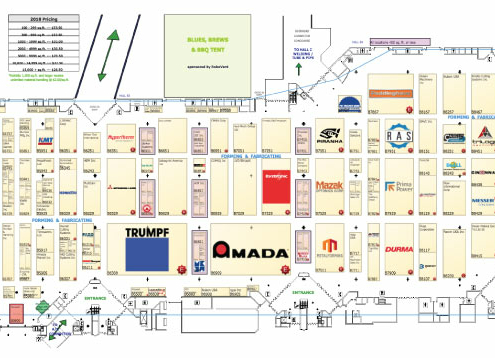
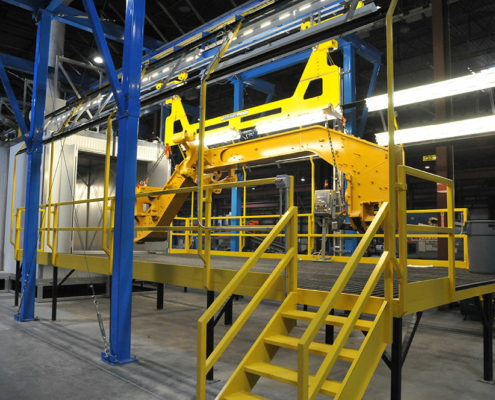
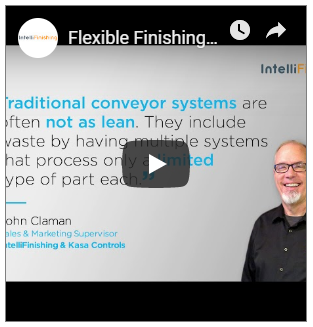
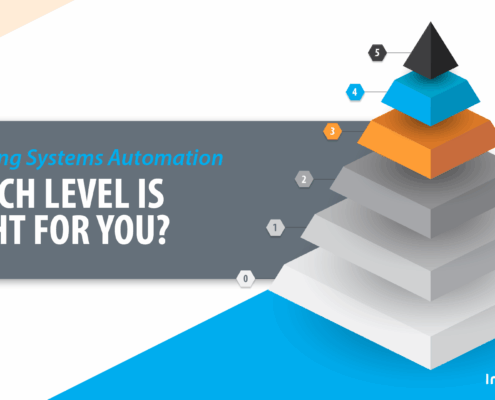
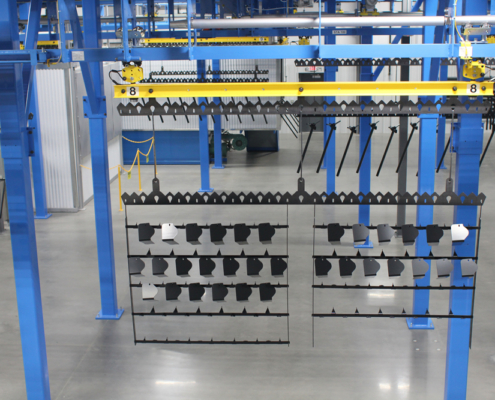
IntelliFinishing Designs Flexible, Modern Powder Coating System for Metal Fabricator, Reducing Costs and Improving Quality
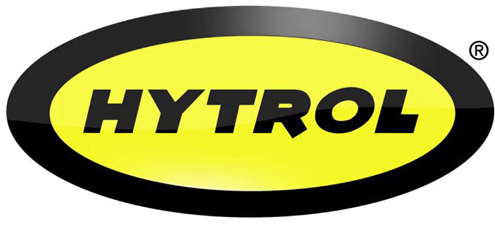
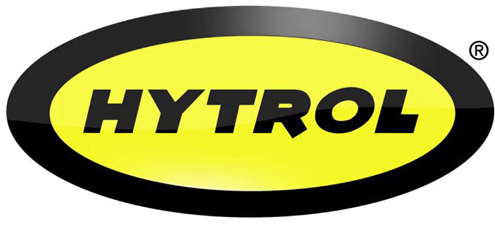